Take advantage of our free tools to uncover the process behind iTLS-ISO™ system for creating intricate lasting change.
iTLS-ISO™ Organization
iTLS™ International Standard Organization (ISO) is the governing and standardization entity that has created the standard body of knowledge for iTLS™® education, implementation and certification worldwide. iTLS-ISO will recognize valid ITLS practitioners using the prescribed body of knowledge of iTLS.
ITLS Study · Evidence Based · Imperically · First Time In The World
Effects of Combined Approach of Theory Of Constraints, Lean and Six Sigma on Process Improvement
iTLS™ Institute®
Become An Expert In Implementation of iTLS
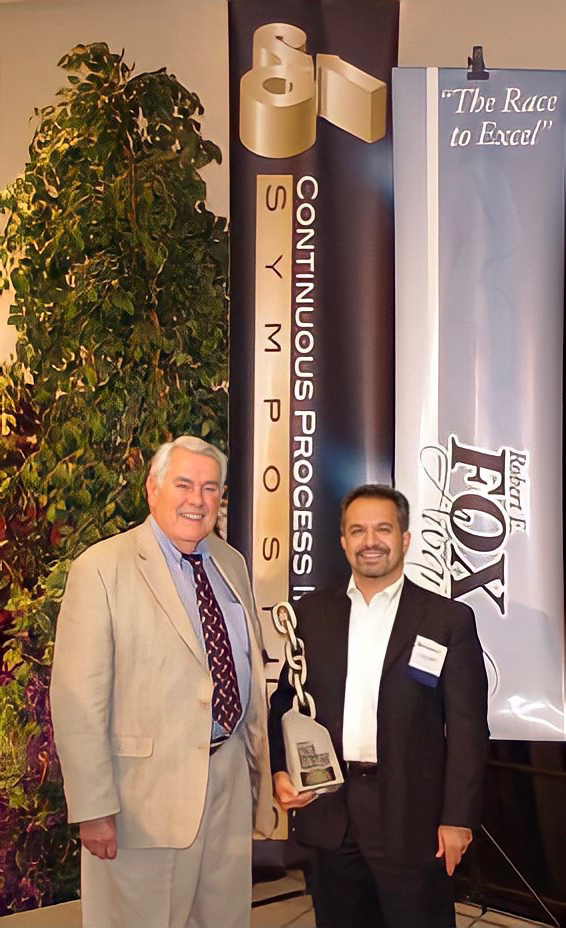
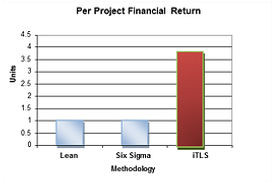
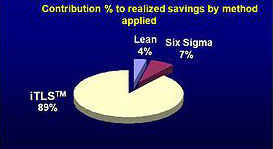
What is iTLS™?
ITLS is new generation of continuous improvement (CPI) model that logically combines three powerful CPI philosophies, their tools and techniques. iTLS harmonizes interaction of Theory Of Constraint, Lean and Six sigma in a synergic mix that optimizes financial results in significantly larger magnitude than if any of these practices where deployed alone. iTLS was developed by Dr. Pirasteh, tested, and documented. Dr. Pirasteh’s findings and application guides are documented in the book, Profitability With No Boundaries.
Implementation of iTLS can improve customer’s experience, lower costs, and build better leaders if it is done right. iTLS accomplishes that by focusing on delivering results through fundamental process knowledge. iTLSapplies common sense, business and scientific tools to improve the processes and products of a company. iTLS has been applied across various disciplines including:
Manufacturing,
Production,
Sales,
Marketing,
Design,
Medical,
Supply Chain Management,
Distribution,
Tele-communication,
Process Industries,
Educations
Administration and Service…
Coaching
iTLS has been applied in various environments nationally and internationally with outstanding results. iTLS has been applied successfully in United States, UK, Brazil, France, Germany, Israel, Mexico, Finland, Canada, India, China, Spain, Ireland, Hungary.
How Does iTLS™ Work?
iTLS is abbreviation for integrated TOC Lean Six Sigma, but there is more to it. iTLSTM is simply a management philosophy that guides you to understand the problems deeply and solve them with more permanent impact. Meanwhile TLS recognizes the existence of natural variability of processes and attempts to control processes statistically within their required specifications. TLS attempts to understand the real problem, priorities, clearly define the real need, and put in place practical solutions; then look for the next improvement opportunity.
iTLS is new generation of continuous improvement (CPI) model that logically combines three powerful CPI philosophies, their tools and techniques. iTLS harmonizes interaction of Theory Of Constraint, Lean and Six sigma in a synergic mix that optimizes financial results in significantly larger magnitude than if any of these practices where deployed alone. Implementation of iTLS can improve customer’s experience, lower costs, and build better leaders if it is done right. iTLS accomplishes that by focusing on delivering results through fundamental process knowledge. iTLS applies common sense, business and scientific tools to improve the processes and products of a company. They are applicable across every discipline including: Production, Sales, Marketing, Design, Administration and Service….
iTLS has been tested in array of environments nationally and internationally with outstanding results. iTLS has been applied successfully in United States, UK, France, Germany, Israel, Mexico, Finland, Canada, India, China, Spain, Ireland, Hungary.
iTLS™ fills the voids and gaps among the existing popular CPI approaches simply and practically. iTLS™ is a process that has been put in practice for over 1,000 projects worldwide and proven to be extremely effective.
iTLS™ is not simply a combination of tools from Lean, TOC and Six Sigma. It is a complete leadership and management system that would help ensure organizations’ quality, profitability, productivity, and continuous improvement of processes with sustained results. This comprehensive system is well explained in the book “Profitability With No Boundaries” authored by Dr. Reza Pirasteh and Robert Fox, published by ASQ.
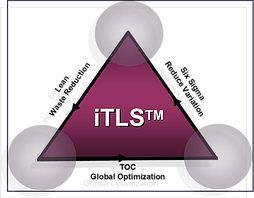
What Was The iTLS™ Evolution Time-line? The following is a brief iTLS™® Brief Time-Line:
1985 – Learn and apply TQM
1996 – Begin to experiment with various combinations of CPI tools
1998 – Developed TLS CPI model (no consensus)
2003 – Documented for the first time in the world:
Quantified effects of Lean, Six Sigma and TLS
2005 – Summarized & documented the designed experiments
2006 – Publicized experiment findings – APICS
2006 –The First CPI Symposium – Weber University – Introduced iTLS · Scott Jensen
2006 – iTLS-Trio model at the Weber University’s CPI symposium
Met Bob Fox and decided on writing a book to ensure integrity of iTLS and possibly bringing the CPI disciplines together for universal betterment…
2007- Introduced iTLS-Trio model at TOC-ICO (Goldratt – Los Vegas)
Others published books based on my research
Created the origin of change in TOC models
2010 – August “Profitability with No Boundaries” available…
Took us 3- years to publish the book – we needed to be sure …
Results of implementations fully supported the model
2012 – Received life-Time Fox Award— Weber University
The iTLS Study — Evidence-Based— First Time In The World Effects of Combined Approach of Theory Of Constraints, Lean and Six Sigma on Process Improvement
By
Reza M. Pirasteh, PhD, MBA, PMP, MBB, CLM
Kimberly Farah, PhD.
Most organizations producing products and/or providing services are faced with urgency of productivity, quality leadership, and higher efficiencies. Customers are asking for cost reductions while at the same time demanding higher quality levels. Companies which are not prepared to respond to their customer requirements and cost parameters could be replaced with domestic or international rival companies that possess these capabilities. The company in this study is a global organization with over 21 plants and 211 team leaders using various process improvement methodologies. The company had over nine customer escalations from their major customers in year 2005, putting their continuing business and credibility in danger.
The company was anxious to find a solution to achieve its goals. It had been using several different process methods including Just In Time (JIT), Lean, Six Sigma and Theory Of Constraints (TOC). Managers had a tendency to use the method they were most comfortable with or had shown the best results for a given type of project. At the upper management level however there was concern that the best management program was not being deployed at each plant location.
Determining which approach or methodology would bring the most effective long-term effect seemed to be an on going challenge for the company. Upper management struggled with the problem which process improvement approach to choose. A decision was made to select among Six Sigma, Lean, or a new method that combined TOC, Lean and Six Sigma (iTLSTM). Management’s goal was to achieve maximum cost savings and quality benefits by selection and adoption of this process improvement methodology.
Initial Conditions
To determine the effectiveness of the three methodologies, an experiment was designed that collected data for over 2 years. The results were statistically analyzed for significance between the three methodologies. The success of each methodology was determined by their aggregate contribution to verifiable financial savings as a result of process improvement projects. These savings were validated with the organization plant controllers and senior management.
iTLS as an alternative approach to continuous improvement was introduced to the company in addition to the existing Lean and Six Sigma, and deployed at several regions as a pilot plan and the results were examined. The data was gathered over 2 years from 21 plants where 211 team leaders had been trained in and were utilizing one of the three methodologies. These plants completed 105 projects cumulatively over the period of the study. The plant management and controllers reviewed these projects for accuracy in claimed improvements, savings and approach. While the results from all projects were documented, the plant personnel and the trainers were not aware of this comparative study as the research was designed in a double blind format to remove potential biases as much as possible.
The goal was to provide the company with data in order to be able to make quantitative decisions and select the process improvement approach that best fit its quality and financial savings requirements. The company measured and tracked a series of process indicators as its key measurements which became drivers for project selections. Some of these measurements were: On-Time Delivery, Warranty Costs and Customer Returns, Inventory Reduction, Cycle Time Reduction and Cost of Scrap.
The team leaders utilized one of the three methodologies mentioned above for improving the plant’s on-time delivery, final quality assurance, customer satisfaction index, warranty costs, and scrap costs. A plant in this study was defined as a production facility that was fully capable of prototyping, designing, producing and distributing customer products located in various regions in the United States. US operations were studied to reduce the impacts of cultural, socio-economical, political and other influences as much as possible on the results. The approach for assigning the plants with a methodology was a natural process due to their local preference, experience with a particular methodology and expertise. The assignment of methodologies was as follows:
· 11 plants applied Six Sigma methodologies
· 4 plants applied Lean.
· 6 plants applied TLS.
Which method is more effective?
In several phone interviews with the trainers and implementers at each region, the authors discussed the three methodologies and asked the trainers the following question: ”Among Lean, Six Sigma or TLS, which of these methods do you believe is more effective?” Trainers responded that his or her approach was most effective according to their personal experience. One senior manager claimed that there were no significant differences between the three methodologies.
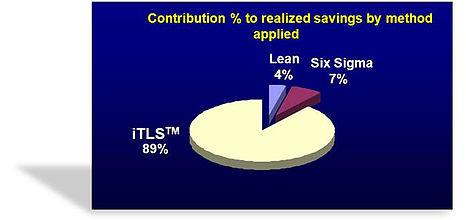
Figure 1 – Contribution % by method applied
Findings
TLS process improvement methodology appeared significantly more effective compared with the other two methodologies, Lean and Six Sigma, by delivering higher cost savings to the company. In this study TLS methodology application resulted in a contribution of 89% of the total savings reported, followed by 7% from Six Sigma and 4% from Lean applications (see figure 1). During this study, 105 projects were completed by the three methodologies. Data indicated that TLS projects delivered on average 2.591 times higher savings that Lean and 3.866 times higher than Six Sigma.
Applying the Method
The TLS model was deployed as a standard approach for continuous process improvements across the organization globally. To assist plant managers in using the TLS method, a general approach was developed by the authors. The sequence of activities begins with application of applying the TOC process to investigate the problem at hand from a 30,000 foot level or satellite-level, which is an approach to measure overall company’s performance (the entire value stream), at a high level (Breyfogle, 2003). After identifying the problem statement at a system level, the mobilized teams develop a specific problem definition that addresses the organization’s bottleneck. At this stage, four steps out of the six-step lean process should be applied (Womack & Jones, 2003). These steps would be:
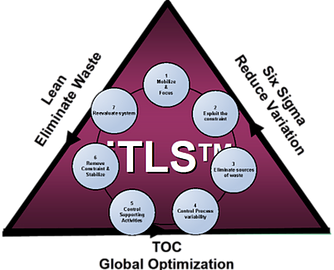
1. Specify the value
2. Identify the value stream
3. Make value flow without any interruptions
4. Let the customer pull value from the producer
By going through steps one through four, the resources of waste in the process would be identified and targeted for improvement.
A parallel approach to implement 5-S at this phase also needs to be considered to bring order and discipline into the process activities. 5-S would also assist in sustaining any process gain achieved and promote continuous improvement as a way of work life. The value-add which is the effort that customer is willing to pay for it, would be identified through the value-stream-mapping process. A waste-less value stream would be considered by streamlining the activities, so that queues and unnecessary inventories and work-in-process would be minimized. By implementing pull systems, the value chain would produce products or services only upon customer requirement. The focus would be to produce the required amount, at the requested time to be delivered to the exact customer and location. After eliminating or minimizing the waste, the new process flow should be established. At this stage, the process input variables need to perform consistently and repeatedly with minimal variability to achieve the best results to minimize waste, scrap, or rework. This leads to steps five and six following the lean process methodology:
5. Pursue perfection
6. Implement with agility
To pursue perfection, Six Sigma’s Define, Measure, Analyze, Implement, and Control (DMAIC), should then be applied to identify and isolate the source (s) of process variation and systematically remove or minimize those variations.
During this stage it may be necessary to perform design of experiments (DOE) to establish the optimal settings for the critical factors that have been identified.
Upon establishing the optimal process variable settings, it is necessary to establish standard operating procedures and control mechanisms to ensure that the process critical factors will remain in statistical control and will not drift over time significantly. Application of Poke-Yoke and statistical process control is essential to sustain the process gains and provide an early warning system to prevent process variability.
A process audit also needs to be designed to monitor process performance over time to ensure that the process gains are maintained. If any deviations are observed during the audit process, they should be the triggers for corrective and preventive action plans.
For further reading
Breyfogle, F. W, III. (2003). Implementing Six Sigma (2nd ed), Hoboken: John Wiley & Sons, Inc.
Goldratt, E. M. (1990). Theory Of Constraints And How Should It Be Implemented, Great Barrington: North River Press Publication Corporation.
Pirasteh, R. M., Horn, S. (2009). The Many Sides Of TLS: Using the TOC, Lean and Six Sigma for Multidimensional Results. APICS. 19(3) 40-43.
Pirasteh, R. M. (2005). Squeezing The MOST Out Of Continuous Improvement: Key To Leadership Principals. APICS. 6(5) 31-33.
Pirasteh, R. M. and Farah, K. (2006). Continuous Improvement Trio: The Top Element of TOC, Lean and Six Sigma Make Music Together. APICS. 16(5) 31-33.
Pirasteh, R. M. (2005) “Effects of Combined Approach of Theory Of Constraints, Lean and Six Sigma on Process Improvement” doctoral dissertation.
Womack, J. P. & Jones, D. T. (2003). Lean Thinking, New York: Free Press.
Summary
Lean and Six Sigma were viable continuous improvement methodologies.
Combining TOC, Lean, and Six Sigma (TLS), resulted in 4X higher benefits than applying each approach individually.
Using TOC, Lean and Six Sigma in proper sequence yielded in higher financial benefits.
iTLS™ approach resulted higher savings per project.